Lighthouses have stood as beacons of hope and guidance along the coastlines for centuries, their lights cutting through fog and storm to ensure the safety of mariners. Among the many materials used in their construction, cast iron has played a significant role, especially in the structural components and intricate detailing. Here, we’ll look at the process of cast iron restoration in lighthouses, the challenges we face, and the meticulous steps we take to preserve these maritime sentinels.
The Role of Cast Iron in Lighthouses
Cast iron became a popular material for lighthouse construction in the 19th century due to its durability, strength, and relative ease of production. It was often used for columns, staircases, railings, and the iconic lantern room where the light is housed. Despite its robust nature, cast iron is not impervious to the ravages of time and the harsh marine environment.
How Cast Iron Components Deteriorate
- Corrosion: The salty sea air is highly corrosive, leading to rust and structural weakness in cast iron components. The constant exposure to moisture and salt accelerates the oxidation process.
- Stress and Fatigue: Over time, the weight and stress on cast iron elements can cause cracking and fatigue, especially in load-bearing parts like columns and beams.
- Mechanical Damage: The wear and tear from regular use, along with potential impacts from storms and other natural events, can damage cast iron fixtures and fittings.
- Poor Maintenance: In some cases, insufficient or improper maintenance over the years can exacerbate the deterioration of cast iron elements.
Steps in Cast Iron Restoration
- Assessment and Documentation
Before any restoration work begins, a thorough assessment of the lighthouse’s cast iron components is essential. This involves visual inspections by a team of experienced experts, and detailed documentation of the condition and any damage. - Removal of Corrosion
The next step is to remove the corrosion from the affected areas. This can be done through various methods, including sandblasting, chemical rust removers, or electrochemical processes. The goal is to strip away the rust without damaging the underlying metal. - Repair and Replacement
Once the corrosion is removed, we assess the extent of the damage. Small cracks and holes can often be repaired with welding or filling materials. For more extensive damage, we may need to fabricate new cast iron components to match the original design. This requires precision and craftsmanship to ensure that the new parts blend seamlessly with the historic structure. - Protective Coatings
To prevent future corrosion, we apply protective coatings to the restored cast iron elements. This typically involves multiple layers of primer, paint, and sometimes specialized coatings designed for marine environments. - Reassembly and Installation
The final step is to carefully reassemble and install the restored or new components. This process requires meticulous attention to detail to ensure that everything fits perfectly and maintains the structural integrity of the lighthouse. - Ongoing Maintenance
Restoration is only part of the equation. Regular maintenance is crucial to preserving the longevity of the restored cast iron. This includes periodic inspections, cleaning, and reapplication of protective coatings as needed.
Case Study: Hunting Island Lighthouse
Hunting Island’s iconic lighthouse was built in 1859 to guide vessels along the coast between Charleston and Savannah and into the Port Royal and St. Helena Sounds. It is one of eight existing lighthouses on the South Carolina coast.
The lighthouse that stands today is not the original as that was detroyed by Confederate soldiers during the Civial War to prevent the Union Navy from using it for navigation. The replica was constructed in 1873 with a special segmented design in case it ever needed to be moved because of erosion.
The lighthouse now sits one and one-quarter miles southwest of its original location. Allen Metals is part of the team working on restoring the historic lighthouse, heading the cast iron restoration of replacing damaged or worn-out cast iron treads, window troughs, replacing the handrail at the watch level, replacing the cornice trim at the watch level, and replacing the port hole at the top of the light house. Duuctile iron support brackets for the cast iron stairs are also being replaced.
detail of original drawings from 1873 and a cast iron stair tread before repair
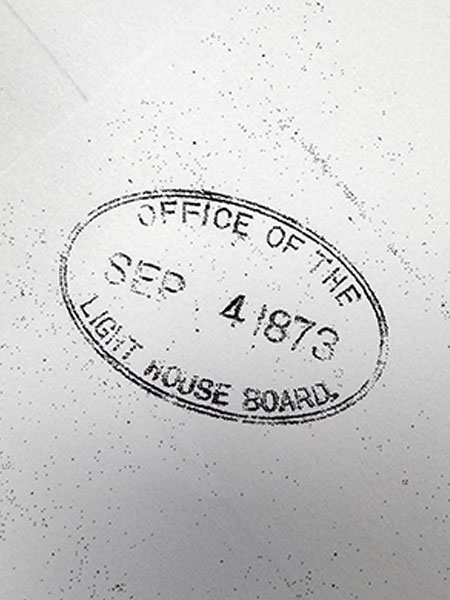
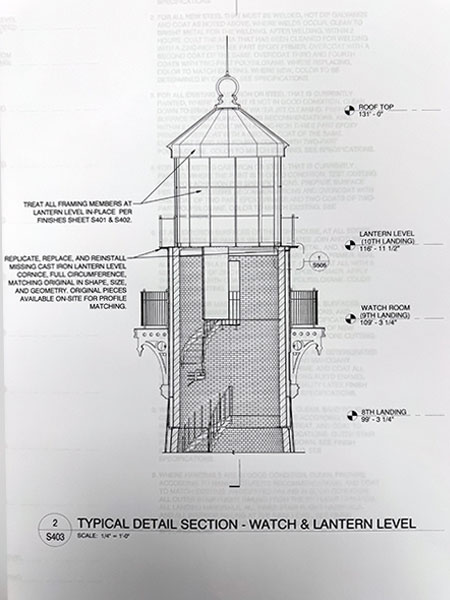
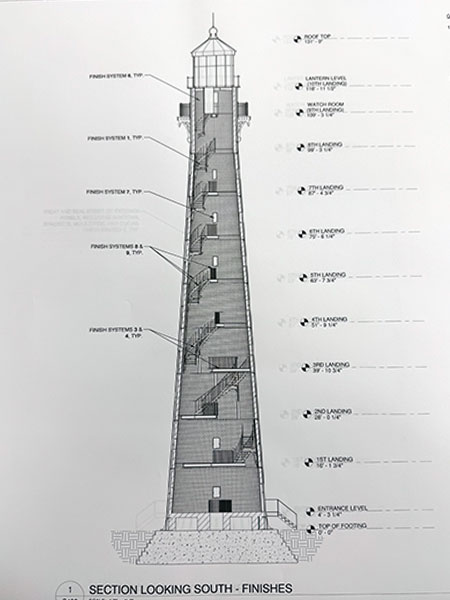
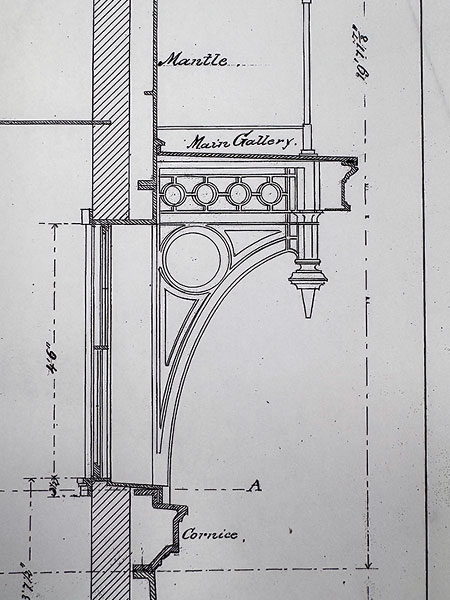
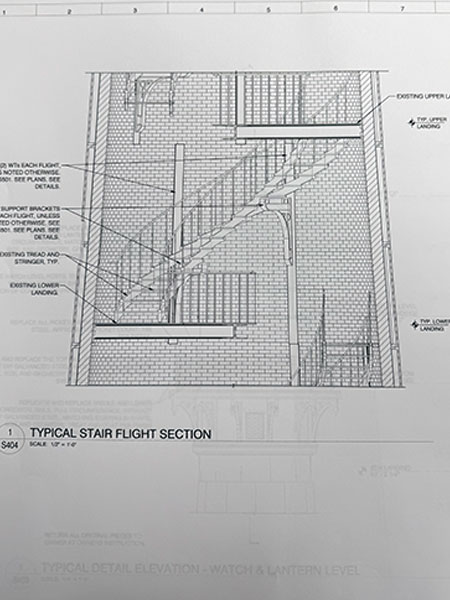
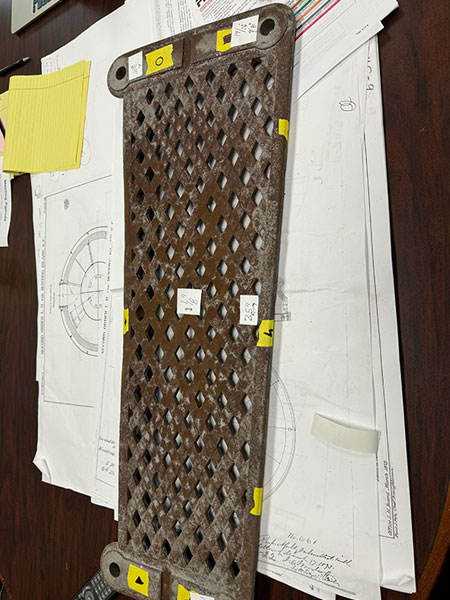
Fun Facts About Hunting Island Lighthouse
- 167 stairs to the top
- Closer to the shore than most lighthouses
- A favorite of visitors
- Can be seen in Forest Gump, GI Jane, and Outer Banks
- The light from the original oil lantern cast a beam of light 17 miles
Preserving Maritime Heritage
Restoring cast iron components in lighthouses is more than just a technical endeavor; it’s a labor of love and a commitment to preserving our maritime heritage. Each project we undertake is a testament to the ingenuity of past builders and the enduring significance of these iconic structures.
By maintaining and restoring lighthouses, we ensure that they continue to stand as symbols of safety and resilience for future generations. Our dedication to quality and craftsmanship ensures that these beacons of light will shine brightly for years to come.